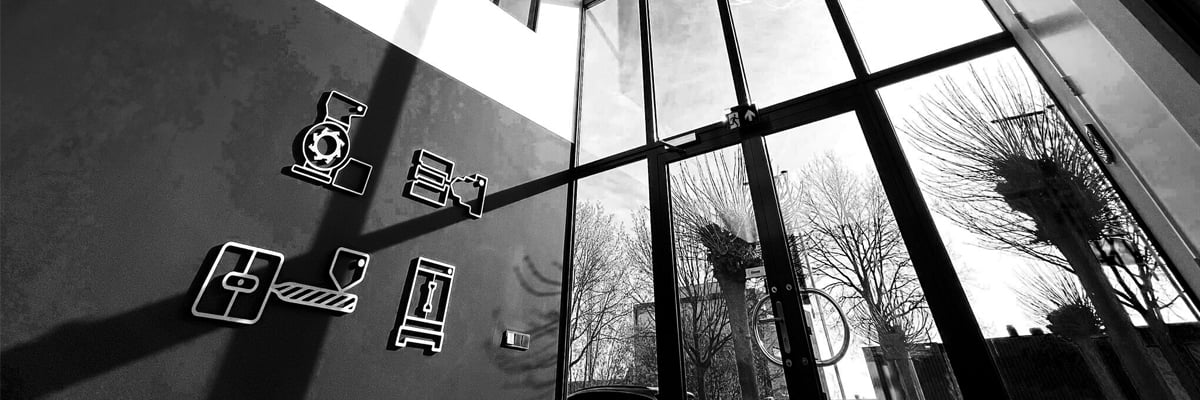
Granulation
Plastima works exclusively with Nordson BKG & Tecnova. These partners provide submerged granulating and water ring granulating. We can therefore provide a total package of high-quality machines for your granulation line.
Granulation
Granulation is a process used to convert plastic waste or resin pellets into small granules or pellets that can be used as raw material in plastic manufacturing processes. The process involves shredding or grinding plastic waste or resin granules into smaller pieces, and then using a machine called a granulator to cut the material into uniform granules or pellets.
The resulting pellets or granules are more manageable and easier to transport than the larger pieces of plastic waste or resin pellets. They can also be more easily melted and formed into new plastic products.
Plastic granulation is an important step in plastic waste recycling, as it enables the transformation of plastic waste into a valuable raw material. The granules or pellets can be used to make new products, reducing the need for new plastic material and reducing the amount of plastic waste ending up in landfills or in the environment.
The quality of the granules or pellets produced by plastic granulation is important because it affects the properties of the final plastic product. The size, shape and composition of the granules or pellets should be carefully controlled to ensure that they meet the requirements of the specific plastic production process in which they will be used.

Types of granulation at Plastima
Water ring granulation
One of the popular plastic recycling machines belongs to the granulation system category. The line system of the plastic water ring pelletiser consists of a mould, a water circulation chamber, a pelletiser, a flushing channel, a centrifugal hydro extruder and a circulating water cooling system.
Granules are melted and discharged through the extruder, then discharged through the mould. During unloading, plastic materials are cut by high-speed rotating blades and the plastic granules are shaken off; after which the granules are cooled and discharged to the water circulation chamber by circulating water film. Using this flushing channel of the water ring pelletising system to transport plastic pellets to the centrifugal extractor can not only prevent the adhesion of the plastic pellets but also acts as a cooling process.
The plastic pellets are generally round-flat, cylindrical or spherical. Plastima works exclusively with Tecnova in this field. For questions about Waterring granulation, please contact us via the contact form below this page.
Tecnova downloads
Underwater granulation
Underwater granulation is used for pelletising different types of polymers, but are especially designed for sticky plastics with a high melt index. Plastic melt coming from the extruder passes the die plate and is immediately cut by the rotating blades. Because water comes into contact with plastic directly at the die plate, underwater granulation is suitable for pelletising almost all types of polymers.
Granules are transferred to the dewatering centrifuge by water in stainless steel tubes. The dimensions of the dewatering centrifuge are designed according to the throughput. Steam fan is used to remove the moist air in the centrifugal freshener generated during dewatering
Thanks to the pelletising technology of underwater granulation, pellets of the same size and shape are continuously cut. Quantity, diameter and geometry of holes on the die plate are chosen based on the type of plastic and throughput. For questions around underwater granulation, Plastima is always at your service!

Contact-information
Contact us