- Home »
- Plastima news »
- Sustainble welding techniques
Sustainable welding techniques for the plastics industry
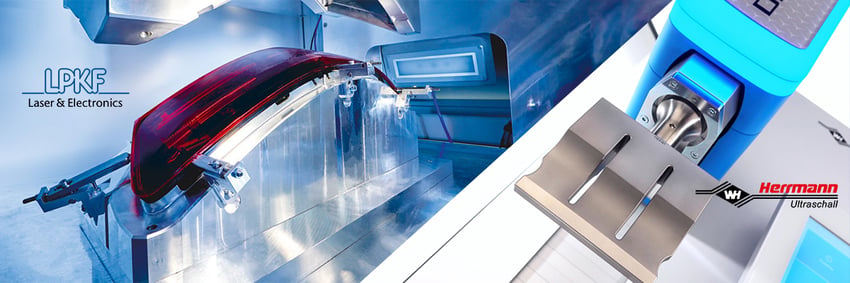
Discover the world of plastic welding with Plastima! In the vast landscape of the plastics industry, welding is not just a technical procedure; it represents a balanced balance of economic strategies mixed with the sophistication of technological innovations.
In this blog, we dive deeper into the topic and also explore the contribution that our welding partners, Herrmann Ultraschall and LPKF Laser & Electronics, can make to your business.
Which forms of welding are good for my product?
Shown above is an ultrasonic welding machine from Hermann Ultraschall
The most durable forms of welding
The advantages of Laser Welding
- Precision and control: Laser welding offers a high degree of precision and is ideal for welding small or complex parts.
- No Physical Contact: There is no direct contact with the workpiece, which minimises the risk of deformation or damage.
- High welding speed: Lasers can weld very fast, which increases productivity.
- Clean Process: It is a clean process with no smoke or splashes, which is beneficial for clean environments.
- Possibility of Automation: Laser welding can be easily automated, promoting consistency and repeatability in mass production.
- Flexibility: Suitable for different types of plastics and can be used for both thin and thick materials.
Pictured above is a laser welding machine from LPKF
The advantages of Ultrasonic Welding
- Low cost: In general, ultrasonic welding has lower operating costs compared to other welding methods.
- Fast and Efficient: The process is fast and efficient, ideal for high production volumes.
- No External Heat Source Needed: Ultrasonic welding generates heat through mechanical vibration, so no external heat source is needed.
- Environmentally friendly: It is an eco-friendly technique without the need for glue, screws, or other consumables.
- Strong Joints: Provides a strong, reliable connection that can withstand pressure and stress.
- Versatility: suitable for welding various types of plastics, including complex and irregular shapes.
Plastima in this plastic-connecting world
At Plastima, we constantly invest in research and development to keep abreast of the latest trends and technologies within the plastic joining market. We understand that every step in the welding process is crucial and that even the smallest details can make a difference. This is why we work closely with our partners, Herrmann Ultraschall and LPKF, to ensure that we can always offer the most advanced and innovative welding equipment and techniques.
In the dynamic and versatile plastics industry, knowledge of the right welding techniques is essential. At Plastima, we understand this like no other. That is why our experts are always ready to answer all your questions about the various welding techniques within this sector. Be it the precision of laser welding, the efficiency of ultrasonic welding, or the versatility of both!