- Home »
- Plastima news »
- Servo hydraulic vs electric
Electric does not always mean more efficient!
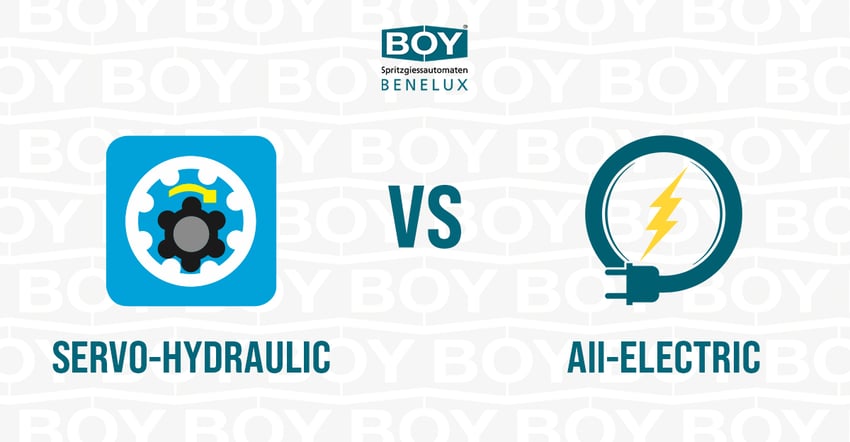
In this blog, we take a closer look at how our partner in injection moulding machines, Dr.Boy GmbH & Co KG, shares its knowledge on drive technologies with the market.
In the world of injection moulding machines, progress is inevitable, and often the future is imagined as all-electric. Many people think that electrification is the ultimate form of technological evolution. This has led to a misconception: that electric machines are always more efficient and durable than servo-driven hydraulic machines, because of their modern appearance.
Another path into the world of technology?
The company Dr.Boy GmbH & Co KG, is a renowned partner in micro, vertical, horizontal and 2-component injection moulding machines. Contrary to the industry trend, which quickly switched to electric technology, BOY has stuck to servo-hydraulics to maintain efficiency. This choice is not based on nostalgia or resistance to change but on a good understanding of the real needs of the industry and the growing demand for energy efficiency in the market.
Shown above is a mould change on a BOY XS
Energy-efficient production has always been a central focus for BOY. They introduced servo-hydraulic pump drives for all machines in the E-series in 2008, pioneering the market. Moreover, all machines in the E-series are equipped with an energy monitor and an energy analysis tool. Which support users in optimising their machine for maximum energy efficiency. This ongoing commitment to energy saving underlines BOY's commitment to sustainable manufacturing practices.
Servo-hydraulic efficiency in an electric world
In a servo-hydraulic machine, only one inverter is needed, and it controls all the different movements such as screw movements, injection movements and so on. This single inverter usually consumes about 100-150 W of power. On the other hand, in all-electric machines, each axis of movement needs its own drive and inverter. For a standard machine (without additional functions such as core pulling), five of these inverters are needed for the basic movements, resulting in a total power consumption of 500-750 W. If the machine also has core pulls, even more inverters are needed, further increasing power consumption.
Beyond glossy brochures and the importance of real data
What these studies show is that we can judge the efficiency of a machine not only by the energy source used but also by how well it performs in the real world. In situations where machines have to work under high pressure and run long hours, Dr Boy's servo-hydraulic technology has repeatedly proved its worth.Shown above is a comparison of energy flow and efficiency (η) between servo-hydraulic and all-electric machines.
In both cases, energy is needed to create the closing force. If we compare the knee lever system of an all-electric injection moulding machine with BOY's clamping system, there is no major difference in the energy required to maintain the closing force. Both systems can maintain the closing force without actively adding energy, so they are both passive.
BOY'S challenge to technological assumptions
Breaking the misunderstanding of electric machines goes beyond technical details; it asks us to rethink our preconceptions and reconsider our ideas of what is modern and old-fashioned. Dr Boy encourages us to focus not only on what is new but also on what is truly better - for our factories, our planet and the future we are building together.
Servo-hydraulic machines tend to have a lower base load than all-electric machines. On the other hand, all-electric machines usually perform better at converting electrical energy into kinetic energy. Which effect is more important depends mainly on the specific production process or object being produced.
For injection moulding processes with low-to-medium material throughput, servo-hydraulic injection moulding machines are more efficient. Measurements show that the total energy consumption of BOY 25 E/BOY 35 E types of machines is usually around 1000-1200 W, which is realistic. For all-electric machines with low-to-medium material throughput, there is mainly a constant base load regardless of the process. In general, servo-hydraulic machines perform better in terms of overall energy efficiency. This can be further improved by using EconFluid hydraulic oil and EconPlast® plasticising cylinders.
BOY'S Conclusion:
The most energy-efficient drive concept depends on the specific process. No single-drive concept is fundamentally better. Servo-hydraulic machines are more efficient at low to medium material throughput, especially up to 1250 kN clamping force. BOY's choice of servo-hydraulic technology shows that true progress is about what works and adds value, regardless of superficial trends. This is true progress.